During the use of newly purchased aluminum profile CNC machining centers, enterprises often need to explore various functions themselves, which increases the difficulty for operators to operate
During the use of newly purchased aluminum profile CNC machining centers, enterprises often need to explore various functions on their own, which increases the difficulty of operation for operators. Today, the editor will teach you a few practical tips to operate with more confidence< Br/>
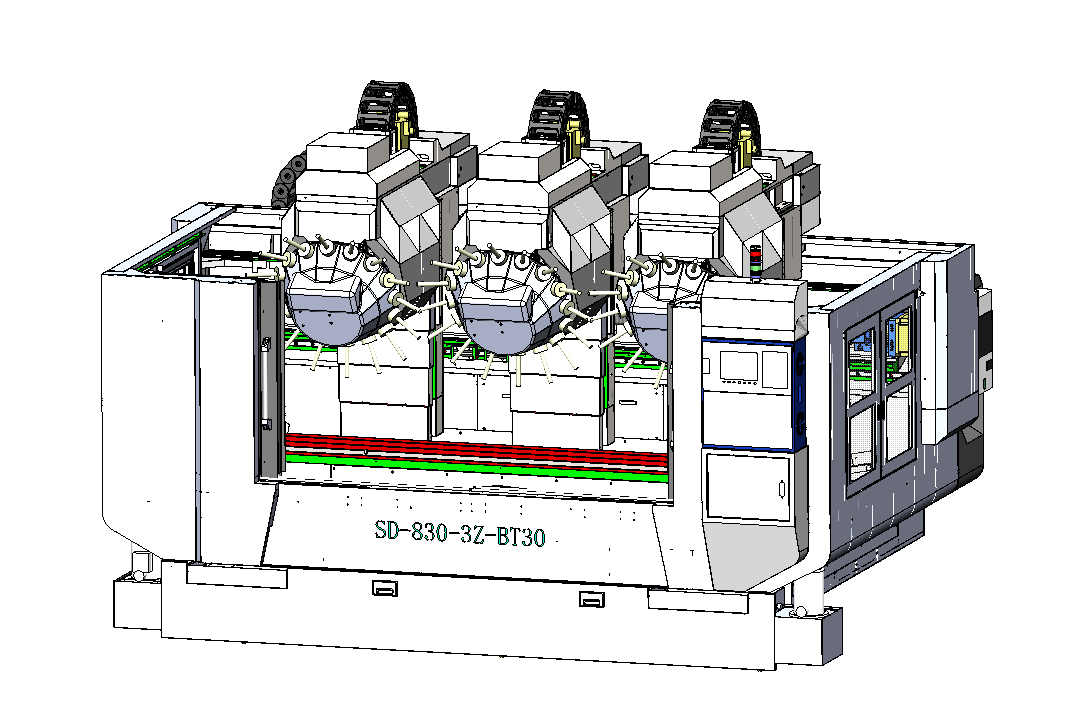
&Nbsp& Nbsp; 1. Computer simulation system
In recent years, with the development of computer technology and the continuous expansion of the CNC machining industry, the number of CNC machining simulation systems has increased significantly, and their functions are becoming increasingly perfect. Therefore, it can be used as a preliminary self inspection program to determine whether collisions will occur by observing the tool's path action< Br/>
&Nbsp& Nbsp; 2. The built-in 3D visualization simulation function of Deli CNC programming software
The Deli CNC aluminum profile processing center equipment is equipped with specially developed programming and processing software, which can display the programmed processing actions. After entering the program, the 3D graphic simulation display function can be called to clearly observe the tool path trajectory, which is used to quickly check whether the tool will collide with the workpiece or fixture< Br/>
(Deli CNC programming software)
3. Slow feed operation of aluminum profile machining center
Check the correctness of the tool path through the slow feed operation of the aluminum profile machining center. After inputting the program into the CNC machining center, clamp the tool or workpiece, then press the run button. At this time, set the feed button to a slower speed, and observe the program trajectory to automatically run. At this time, you can observe whether the spindle may collide with the workpiece or fixture. In this case, it is necessary to ensure that the tool cannot be loaded when the workpiece is loaded; When installing cutting tools, the workpiece cannot be installed, otherwise collision may occur< Br/>
&Nbsp& Nbsp; 4. The coordinate system and tool compensation settings are correct
Before starting the profile CNC machining center, it is necessary to set the corresponding reference points. The working coordinate system of the profile CNC machining center should be consistent with the programming, especially the Z-axis direction. If it is not consistent, the possibility of the milling cutter colliding with the workpiece will be very high. In addition, the length compensation set for the tool should be ensured to be correct, otherwise it will either be empty machining, over cutting, or collision< Br/>
&Nbsp& Nbsp; 5. Improve programming skills
Programming is also a very important part of CNC machining. Mastering programming skills proficiently and observing it several times before starting the program can greatly avoid unnecessary collisions< Br/>
For example, when milling the inner cavity of a workpiece, after the milling is completed, it is necessary to