The utility model relates to a workpiece processing equipment, specifically a motor shaft hole processing equipment.
The utility model relates to a workpiece processing equipment, specifically a motor shaft hole processing equipment< Br/>
Background technology:
The motor shaft is an important component of motor products, and the machining accuracy and quality of the motor shaft directly affect the overall quality and service life of the motor. As shown in Figures 1a to 1b, traditional motor shaft products usually use ordinary lathes to process the tapered holes at the tail end through manual operation, which requires manual loading into the fixture. This has poor stability, low efficiency, and is prone to scrap, resulting in high scrap rate, low processing accuracy, and high labor intensity. The main drawbacks can be divided into two aspects:
In terms of supply
1. Low efficiency: Due to frequent repetitive labor causing fatigue, a person's mental state can also affect production efficiency, thus affecting the efficiency of material supply< Br/>
2. High scrap rate: Due to the positive and negative direction of the product, if the operator is negligent, it will cause scrap, and external influences will also cause the operator to be distracted< Br/>
3. Unable to work continuously for long periods of time: manual operations will inevitably have rest time, resulting in equipment shutdown< Br/>
4. Low accuracy: Manual operation is not as stable as machine operation, which can easily cause dimensional deviation< Br/>
In terms of processing
1. Unable to process continuously. After each workpiece is processed, it needs to be removed and then clamped. Processing cannot be carried out continuously, with long intervals, high labor intensity, and low production efficiency< Br/>
2. The equipment has poor stability, large size deviation, and is prone to exceeding the tolerance, resulting in waste products< Br/>
3. The clamping efficiency of the chuck is low and cannot meet the needs of continuous operation< Br/>
4. The processed workpiece needs to be manually cut, which wastes a lot of time< Br/>
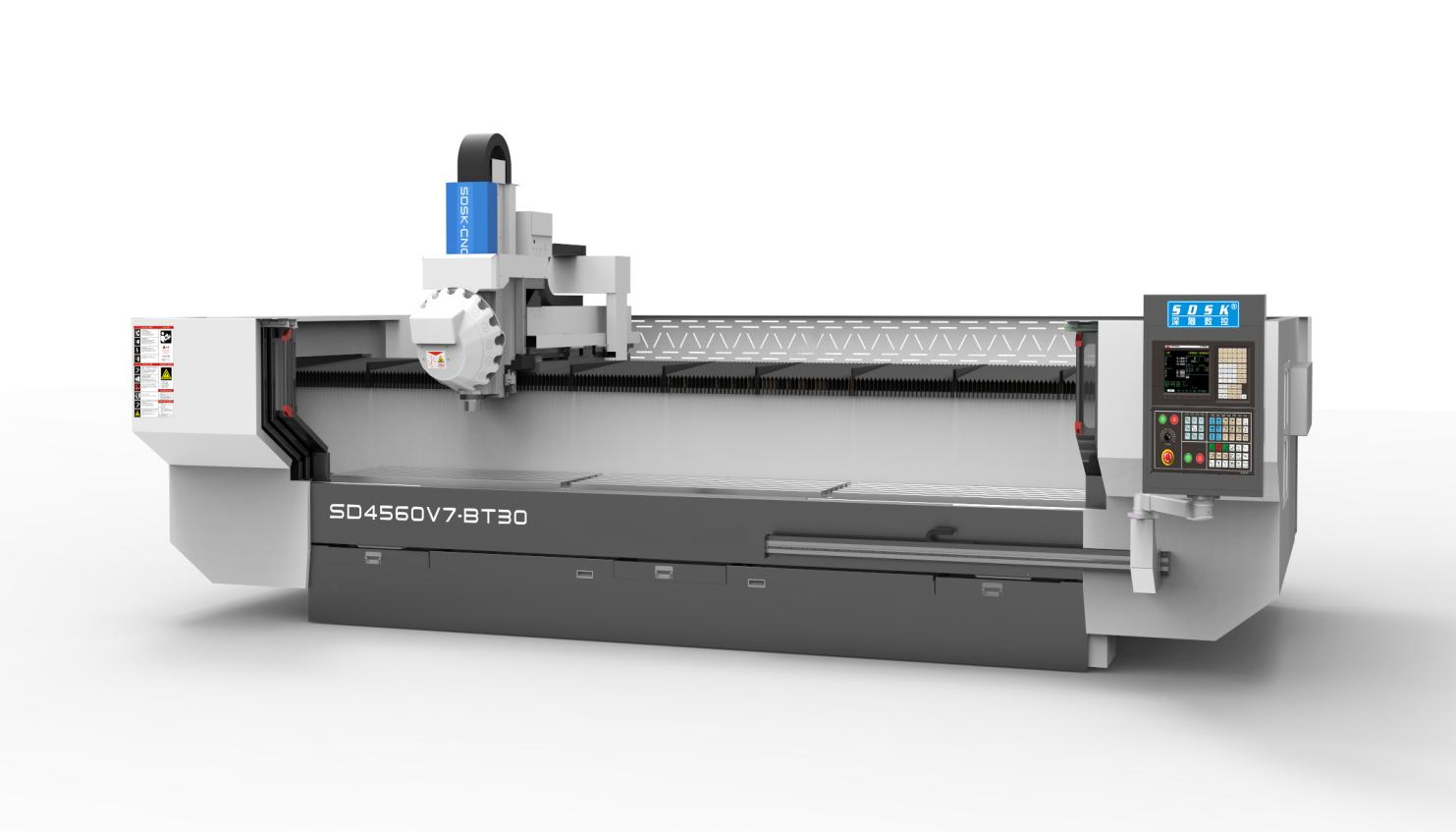
Technical implementation elements:
In response to the shortcomings of high labor intensity and low efficiency in the machining process of the tapered hole at the tail end of the motor shaft product in the existing technology, the present utility model aims to solve the problem of providing a motor shaft hole machining equipment that can automatically load and unload materials, process continuously, and greatly improve work efficiency< Br/>
To solve the above technical problems, the technical solution adopted by this utility model is:
This utility model relates to a motor shaft hole processing equipment, which includes a bed body, a mechanism body, a cutting fluid box, a spindle cooling fluid box, and a distribution box. The mechanism body is installed on the bed body, the distribution box is installed on one side of the bed body, and the cutting fluid box and the spindle cooling fluid box are installed in the bed body; The institutional body includes feeding components, drilling components, station conversion components, and transmission components