Aluminum profile processing is a new processing technology - its working principle is to develop simple processing programs - convert manual operations into computer programming - and then combine with simple manual processing
Aluminum profile processing is a new processing technology, which works by programming a simple processing program, converting manual operations into computer programming, and then combining it with simple manual processing. Improve the efficiency of aluminum profile manufacturers in the production and processing process, and save labor costs. The aluminum profiles processed by CNC milling machines using aluminum profiles have high precision and can meet the requirements of most enterprises with high precision requirements for aluminum profiles< Br/>
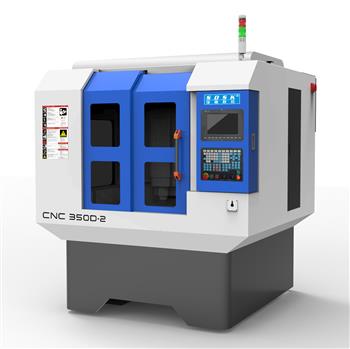
So, what are the misconceptions about aluminum profile processing< Br/>
1. Fast forward and work forward
In the aluminum profile processing program, both G00 and G01 can define the linear motion of the cutting tool, but their functions are very different and beginners can easily confuse them< Br/>
The feed rate of work-related instructions (G01, G02, G03, etc.) is determined by the F instruction in the program; The feed rate of fast forward commands (G00 and partial zero return commands) is not specified in the machining program, but is saved as machine parameters in the CNC system during machine parameter settings< Br/>
Engineering instructions not only need to ensure the accuracy of the machining end point, but also the accuracy of the machining path and feed rate, which requires micro level interpolation calculation and dynamic control to achieve< Br/>
The purpose of fast forward commands is to minimize idle travel time, and in multi axis linkage, the motion trajectory is unpredictable. Therefore, fast forward commands cannot be used for machining feed< Br/>
2. Positioning accuracy and repeated positioning accuracy
Manufacturing center manufacturers often only provide repeated positioning accuracy without providing positioning accuracy indicators in promotional materials, which makes it easy for some users to misunderstand repeated positioning accuracy as the main indicator determining the machining accuracy of parts. In fact, high repeated positioning accuracy does not necessarily mean high machining accuracy of the parts. Positioning accuracy is the main indicator that determines the machining accuracy of parts< Br/>
The precision of repeated positioning reflects the ability of the machine tool to return to the same position multiple times. The measurement method is to fix a dial gauge, press the gauge head on the spindle, and calibrate the zero point of the dial gauge. Move the spindle to any position and return it to the previously calibrated coordinate position, then read the dial gauge reading error. After multiple round trips of readings, the maximum error obtained is the repeated positioning accuracy< Br/>
Aluminum profile processing follows the current level of CNC technology and typical electromechanical matching of machining centers, that is, servo motors+rotary encoders+ball screws or gear racks. The repeated positioning error is generally not more than 2 pulse equivalents, far less than 0.01mm< Br/>
Positioning accuracy refers to the ability to accurately move a specified distance across the entire range of a machine tool. The maximum stroke of the aluminum profile processing center can reach 7 meters, and the positioning accuracy measurement is generally carried out using a laser interferometer< Br/>
The positioning accuracy is mainly affected by the shape and position error of the guide rail, as well as the machine